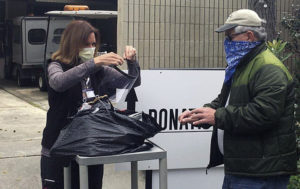
Jim Costa delivers medical face shields to Anne Marie Taylor of John Muir Medical Foundation. (Photo – Jeff Garberson)
A small Livermore group with experience in business, engineering, manufacturing and entrepreneurship is responding to the needs of regional medical providers who lack personal protective equipment during the COVID-19 crisis.
Within just a few days of sharing ideas online and by telephone, the group manufactured and delivered 100 face shields to John Muir Medical Center in Walnut Creek. It expects to deliver 100 more in the near future.
Learning that Contra Costa County emergency services foresees a shortage of medical isolation gowns, the group identified a Bay Area company idled by emergency closure rules that can repurpose manufacturing equipment to make thousands of them.
The group grew out of a discussion between Livermore neighbors and colleagues who realized that they and their friends should be able to provide stopgap supplies to medical workers who need protective gear while treating contagious COVID-19 patients.
The neighbors were Jim Costa, a retired Sandia engineer; and Karen Burns, a partner in the accounting firm Sensiba San Filippo and a founder of the Association of Manufacturers-Bay Area.
Costa has extensive ties with Livermore’s rich technical community, Burns with the world of manufacturing.
Colleagues included managers, designers, engineers, experts at fabrication and people who knew how to build things using tools like 3D printers and laser cutters.
Many were volunteering already or were happy to do so at a time of reduced or absent workloads.
They connected with i-GATE and Innovation Tri Valley Leadership Group, creating avenues to wider communities. I-GATE is Livermore’s entrepreneurial and start-up hub, led by executive director Brandon Cardwell. Innovation Tri Valley, led by CEO Lynn Naylor, links business and technology leaders across the Tri Valley.
At the Livermore Lab Foundation, which supports research at Lawrence Livermore National Laboratory, president Dona Crawford reached out to one of the Foundation directors, Catharine Baker, the former Assemblywoman.
Baker connected the group with the John Muir Medical Center, where they learned of the need for face shields. She also advised them of the long term need for isolation gowns as foreseen by Contra Costa emergency services in the event of a surge of COVID-19 cases.
For the face shields, Drew Felker, a Livermore entrepreneur, developed designs based on online information. He then contacted a friend, Steve Traugott, whose company had a laser cutter that could slice plastic sheets into appropriate sizes and shapes.
After a few trial runs, Felker and his wife began assembling the masks. “I’m just a local guy who likes to get things done,” he said in a telephone interview. His electrical inspection business, TruTech Energy Services, is idled by home shelter regulations.
Traugott’s company, CD International Technology, produces high quality electronics systems and components for use in demanding industries, like research, defense and medicine.
Located in the industrial park just north of Lawrence Livermore National Laboratory, it, too, is idled by shelter regulations, although it is able to respond on demand, according to the company website.
To respond to Contra Costa County’s anticipated need for large numbers of protective medical gowns, sometimes called isolation gowns, Burns made use of a state database of manufacturers who are willing to help with the COVID-19 crisis. The database is maintained by the California Manufacturers and Technology Association.
Identifying a Santa Clara manufacturer that indicated it could help with the request for 30,000 gowns, she then put the company directly in touch with appropriate Contra Costa County authorities.
“There’s no reason for us to remain in the middle,” Burns said. “We want to get the right people together at the right time and let them take it from there.”
Although the group remains informal, it now calls itself the Tri Valley Together Volunteer Response Network. Information is available through Innovation Tri Valley at [email protected]; it is working on an updated website.
In the meantime, leaders emphasize that they are operating at two levels: offering small quantities of medical supplies that can be made with local skills, and facilitating communications at a somewhat larger scale between regional suppliers and medical end users.
The ultimate goal is to help local and regional medical systems on a stopgap basis while national manufacturers get their production lines up and running.
“It can be difficult for the major manufacturers to turn on a dime,” Burns said.
According to i-GATE’s Cardwell, the organizational goal was to “collect local small batch prototype and manufacturing people who could make 20, 30, 100 of something” while Burns explored her connections to regional and national manufacturers “who can solve a problem at scale.”
Cardwell credits the Tri Valley cities, the national labs and other organizations that have invested time and energy in fostering an entrepreneurial culture and building links between technical organizations through Innovation TriValley and i-GATE.
“Leadership coming out of local, regional and state governments is what has given us the bandwidth to solve some of these problems,” he said. “Otherwise we’d be experiencing same kinds of inundation that New York, New Jersey and some of the other hot spots have been dealing with.”